?在
鋁盒生產過程中,折彎是一個關鍵環節,以下是需要注意的細節:
?
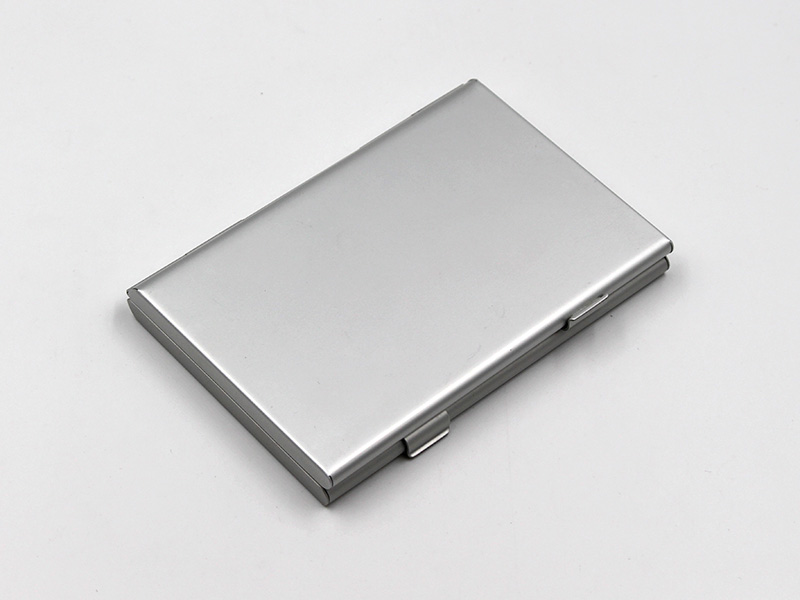
一、折彎前的準備
材料檢查
材質確認:明確鋁盒所使用的鋁材型號,如 1 系純鋁(如 1060)、3 系鋁錳合金(如 3003)或 5 系鋁鎂合金(如 5052)等。不同型號的鋁材具有不同的機械性能,像 5052 合金鋁的強度和耐腐蝕性相對較高,在折彎時所需的壓力和折彎系數與 1060 純鋁有所不同。
厚度測量:使用卡尺精確測量鋁材的厚度,確保厚度符合鋁盒設計要求。一般鋁盒生產所用鋁材厚度在 0.3 - 2.0mm 之間,厚度公差通??刂圃?±0.05mm 以內,因為厚度會直接影響折彎模具的選擇和折彎參數的設定。
表面質量檢查:檢查鋁材表面是否有劃痕、氧化膜、油污等缺陷。表面劃痕可能會在折彎過程中成為應力集中點,導致鋁材斷裂;氧化膜過厚可能影響折彎效果,需要進行適當的預處理;油污會使鋁材與模具之間的摩擦力減小,可能導致鋁材在折彎過程中移位,所以要確保鋁材表面干凈整潔。
模具準備
模具選型:根據鋁材的厚度、材質和鋁盒的折彎形狀來選擇合適的折彎模具。模具的 V 形槽寬度一般是鋁材厚度的 5 - 8 倍,例如,對于 1mm 厚的鋁材,V 形槽寬度可選擇在 5 - 8mm 之間。同時,要考慮模具的上模(凸模)和下模(凹模)的圓角半徑,其應與鋁盒設計的折彎內圓角相匹配,一般模具圓角半徑在 0.5 - 2.0mm 之間。
模具安裝與調試:在安裝模具時,要確保模具安裝牢固,上下模的中心線對齊。安裝完成后,使用塞尺檢查模具間隙,間隙應均勻,通常為鋁材厚度的 0.1 - 0.15 倍。例如,對于 0.5mm 厚的鋁材,模具間隙應在 0.05 - 0.075mm 之間。調試模具時,可以先進行試折彎,觀察折彎效果,對模具位置和參數進行微調。
設備檢查
折彎機功能檢查:檢查折彎機的滑塊上下運動是否順暢、速度是否均勻,后擋料裝置的定位精度是否符合要求,液壓系統或機械傳動系統是否正常工作。啟動折彎機,觀察是否有異常噪音或振動,確保設備處于良好的工作狀態。
設備精度校準:使用專業的量具對折彎機的關鍵精度指標進行校準,如滑塊與工作臺的垂直度、后擋料裝置的定位精度等?;瑝K與工作臺的垂直度誤差一般要求在 ±0.1mm/m 以內,后擋料裝置的定位精度應達到 ±0.05mm。對于數控折彎機,還要檢查數控系統的參數設置是否正確,程序是否能夠正常運行。
二、折彎過程中的操作要點
工件定位
放置位置精確性:將鋁材準確地放置在折彎機的工作臺上,使其與后擋料裝置緊密貼合。對于有定位孔或定位標記的鋁材,要按照設計要求進行定位。工件放置位置的誤差應控制在 ±0.5mm 以內,以保證折彎位置的準確性。
方向確認:明確鋁材的折彎方向,特別是對于有多個折彎工序的鋁盒,要嚴格按照加工圖紙的要求依次確定每個折彎的方向。對于形狀復雜的鋁盒,可能需要制作簡單的夾具輔助定位,確保鋁材在折彎過程中不會發生位移。
折彎參數設置
折彎角度設定:根據鋁盒的設計圖紙,在折彎機的數控系統或操作面板上精確設置折彎角度。考慮到鋁材的回彈特性,一般需要進行試折彎來調整角度補償值。對于精度要求較高的鋁盒,折彎角度誤差通??刂圃?±0.5° 以內。不同型號的鋁材回彈量不同,例如,1060 純鋁的回彈量相對 3003 合金鋁可能更大,需要根據實際情況調整折彎角度。
壓力調節:依據鋁材的厚度、材質和折彎長度來設置合適的折彎壓力。壓力過小可能導致折彎不完全,出現折痕不明顯或角度不到位的情況;壓力過大則可能會損壞模具和鋁材??梢詤⒖颊蹚潤C的壓力參數表,并結合實際試折情況進行調整。一般來說,隨著鋁材厚度和強度的增加,所需的折彎壓力也相應增大。
折彎速度控制:合理控制折彎速度,避免速度過快或過慢。速度過快可能會引起鋁材表面的劃傷、模具的磨損加劇,以及產生較大的振動和噪音;速度過慢則會影響生產效率。對于大多數鋁盒生產,折彎速度可設置在 5 - 10mm/s 之間,但具體速度還需要根據鋁材特性和折彎復雜程度進行調整。
操作執行與監控
首次試折:在正式批量折彎之前,進行試折操作。觀察試折后的鋁盒折彎角度、尺寸、表面質量等是否符合要求。如果有不符合的情況,及時調整折彎參數,如角度、壓力、速度等。試折數量一般為 1 - 3 件,直到確定出合適的折彎參數。
連續折彎操作:在試折合格后,進行批量折彎。在操作過程中,要密切觀察鋁材的折彎情況,包括折彎角度的一致性、表面質量、是否有裂紋等缺陷。每折彎一定數量的鋁材(如 10 - 20 件)后,要重新檢查折彎角度和尺寸,防止因模具磨損、鋁材批次差異等因素導致折彎質量下降。
多人協作注意事項:如果是多人協作進行折彎操作,要明確各操作人員的職責,確保操作的同步性和安全性。例如,在大型鋁盒或復雜形狀鋁盒的折彎過程中,需要有人負責操作折彎機,有人負責協助定位和搬運鋁材,操作人員之間要保持良好的溝通,避免因操作不協調而引發事故。
三、折彎后的檢查與處理
質量檢查
尺寸精度檢查:使用卡尺、角度尺等量具對折彎后的鋁盒尺寸進行檢查,包括折彎角度、邊長、高度等尺寸。將測量結果與加工圖紙進行對比,對于不符合尺寸要求的鋁盒,要分析原因并進行調整。例如,若折彎角度偏差超過允許范圍,可以通過調整折彎機的角度補償參數來修正。
表面質量檢查:檢查鋁盒表面是否有劃痕、壓痕、裂紋等缺陷。表面劃痕可能是由于模具表面不光滑或鋁材在折彎過程中與其他物體摩擦引起的;壓痕可能是壓力過大或模具間隙不合適造成的;裂紋則可能是鋁材本身質量問題或折彎參數不當導致的。對于有表面質量問題的鋁盒,要根據具體情況進行修復或報廢處理。
形狀檢查:檢查鋁盒的整體形狀是否符合設計要求,特別是對于有復雜形狀的鋁盒,要檢查各個折彎部位之間的銜接是否平滑、過渡是否自然。如果發現形狀不符合要求,可能需要重新調整折彎工藝或對鋁盒進行整形處理。
后續處理
去毛刺處理:折彎后的鋁盒邊緣可能會產生毛刺,使用銼刀、砂紙或專用的去毛刺工具將毛刺去除。對于要求較高的鋁盒,還可以采用化學去毛刺或電化學去毛刺等方法,以獲得更好的表面質量。
清洗與表面處理:如果鋁盒在折彎過程中沾染了油污、冷卻液等雜質,需要進行清洗??梢允褂煤线m的清洗劑進行清洗,然后根據鋁盒的最終用途進行表面處理,如陽極氧化、噴漆等,以提高鋁盒的耐腐蝕性和美觀度。